Tecnología MIM
METAL INJECTION MOLDING
ventajas de dos mundos
Los componentes en serie con formas complejas de metal conllevan, en la mayoría de los casos, una producción muy costosa. Pero, afortunadamente, con la tecnología MIM de Zimmer Group existe ahora una alternativa ventajosa para las piezas de trabajo que normalmente requieren un gran esfuerzo para su fabricación.
Con el proceso MIM producimos piezas metálicas de casi cualquier forma deseada mediante el proceso de moldeo por inyección, con la misma facilidad que si se tratara de plástico. Además, combinamos con total elegancia la libertad geométrica de la inyección de plástico con las excepcionales propiedades de resistencia y desgaste de los metales.
El resultado es una tecnología para la fabricación en serie de componentes metálicos de formas complejas, que convence en todos los aspectos, y a unos precios muy atractivos.
As a result, MIM technology offers you a host of appealing advantages:
- As a result, MIM technology offers you a host of appealing advantages:
- Cost-effective series production of metallic workpieces
- Entirely new level of freedom for designing parts
- Combines the advantages of injection molding technology with the outstanding strength and wear characteristics of metals
- Series production of smaller components with weights from 0.3 g to 150 g
- Complex components with a wall thickness down to 0.2 mm
- Ability to implement small and large holes, inner and outer threading, cross holes, undercuts and gear teeth
- Full utilization of the strength properties of the material being used
- Mechanical strength of workpieces equal to conventional manufacturing processes
- Surface treatment using frictional grinding, mirror polishing, sandblasting, passivation, electropolishing or etching
- Coating using burnishing or plating with chrome, copper, nickel, silver or gold
- Avoids production costs and the use of expensive assembly and connection techniques
- Significantly lower costs for complex components
- 25% to 65% less expensive than conventional production processes
- Applicable in a vast assortment of areas: Gearbox parts, watches, jewelry, eyeglass parts, surgical instruments, tweezers, dental braces, small and micro-sized parts for mobile phones, computers or other devices
Material properties-PDF
MIM El proceso
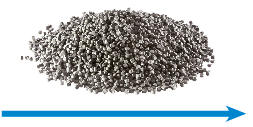
Materia prima
El material original para el moldeo por inyección de polvo metálico constituye el llamado "feedstock" o materia prima. Éste se compone aprox. en un 60 % de polvo metálico correspondiente, y en un 40 % de partículas lubricantes y plastificantes (polímeros, termoplásticos, componentes orgánicos). Es muy importante una mezcla homogénea de todos los componentes, porque solo así se garantiza en el siguiente paso su procesamiento óptimo y una calidad estable del producto.
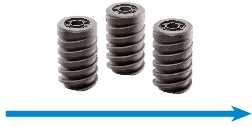
Moldeo por inyección
La materia prima se inyecta de manera análoga al granulado de plástico de las inyectoras. La parte del aglutinante se derrite a elevadas temperaturas, y la masa viscosa resultante de polvo de metal y aglutinante, se inyecta a continuación en el molde de la pieza correspondiente. Las piezas que se obtienen son las llamadas "piezas verdes", que deben transformarse en procesos posteriores en piezas puramente metálicas.
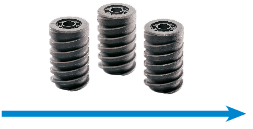
Desbanderizado
En el paso del desbanderizado de la "pieza verde" se extrae la parte principal del aglomerante. Normalmente esto se produce mediante la eliminación del aglomerante, con un disolvente o por una reacción catalítica. Lo que queda es una pieza porosa que se mantiene unida gracias a los residuos del aglomerante. El desbanderizado restante de estas piezas, que se suelen llamar "piezas marrones", se realiza térmicamente en un horno. Esto significa que, a una temperatura elevada de entre 400 °C y 900 °C, se evapora el aglomerante residual. Al mismo tiempo, las partículas de metal empiezan a unirse formando los llamados "cuellos de sinterización". Éstos proporcionan a las piezas la suficiente estabilidad para el siguiente paso de sinterización.
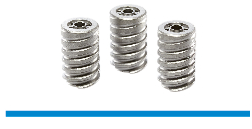
Sinterizado
El último paso del proceso, la sinterización, cierra los poros que ha dejado el aglomerante. Las piezas se compactan a unas altas temperaturas que superan normalmente los 1000 °C. La temperatura necesaria del horno de sinterizado depende en gran medida del material y de la geometría de la pieza. Por este motivo, este paso debe adaptarse o desarrollarse para cada geometría y para cada material de manera individual. Con ello le garantizamos una calidad óptima de las piezas durante todo su ciclo de vida.
Formulario de consulta
Metal injection molding - MIM
Tiempo de tramitación de las ofertas
- Piezas de plástico - en un plazo de 3 días laborables*.
- Piezas MIM - en un plazo de 3 días laborables*.
- Herramientas de moldeo por inyección (plástico/MIM) - en 3 días laborables*.
- Cambios de herramientas: en un plazo de 3 días laborables*.
- Servicios (fresado, torneado, erosión) - en un plazo de 3 días laborables*.
*Requisito: el diseño de los componentes está terminado o liberado.