WWR50F-B
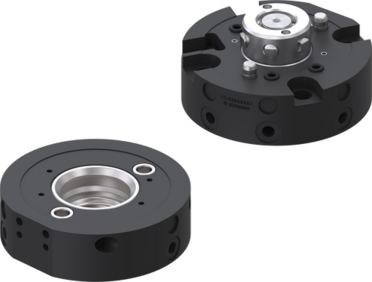
Tool Changers
Series WWR
- Secure hold during pressure drop
The combination of spring loaded and a high gear ratio guarantees them a safe machine - Extremely flat design
This structure reduces the moment load for your robot to a minimum and makes it possible to use smaller and more affordable sizes - Inexhaustible variety of media transfer systems
No matter which medium you would like to transmit, we will draw from our wealth of experience in implementing projects and find a solution to suit your needs!
Technical Data
Connecting flange according EN ISO 9409-1 | TK 50 |
Pneumatic energy transfer | 4 [Quantity] |
Flow per connector | 150 [l/min] |
Electrical energy transfer | optional |
Self locking mechanism when locking | mechanical |
Locking stroke | 0.3 [mm] |
Repetition accuracy in Z | 0.01 [mm] |
Repetition accuracy in X, Y | 0,02 [mm] |
Joining force | 50 [N] |
Release force | 30 [N] |
Offset at coupling max. in X,Y | 1.5 [mm] |
Operating pressure | 4 ... 10 [bar] |
Nominal operating pressure | 6 [bar] |
Operating temperature | 5 ... +80 [°C] |
Air volume per cycle | 3 [cm³] |
Moment of inertia | 0.8 [kgcm²] |
Weight | 0.2 [kg] |
Recommended handling weight | 30 [kg] |
Accessory
Benefits in detail
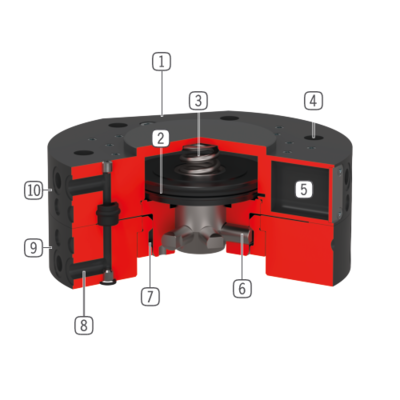
- Mounting for energy element
- Drive
double-acting pneumatic cylinder - Integrated spring
energy storage in case of drop in pressure - Robot flange
partial mounting circle in accordance with EN ISO 9409-1 - Piston position sensing
via magnetic field sensor - Locking bolt
adapted to the clamping sleeve - Locking sleeve
high moment capacity - Integrated air feed-through
Air / vaccum transfer Hoseless control possible - Loose part
For tool side assembly - Fix part
For robot side assembly